Concrete Takeoff: The Ultimate Guide to Estimating your Next Concrete Job
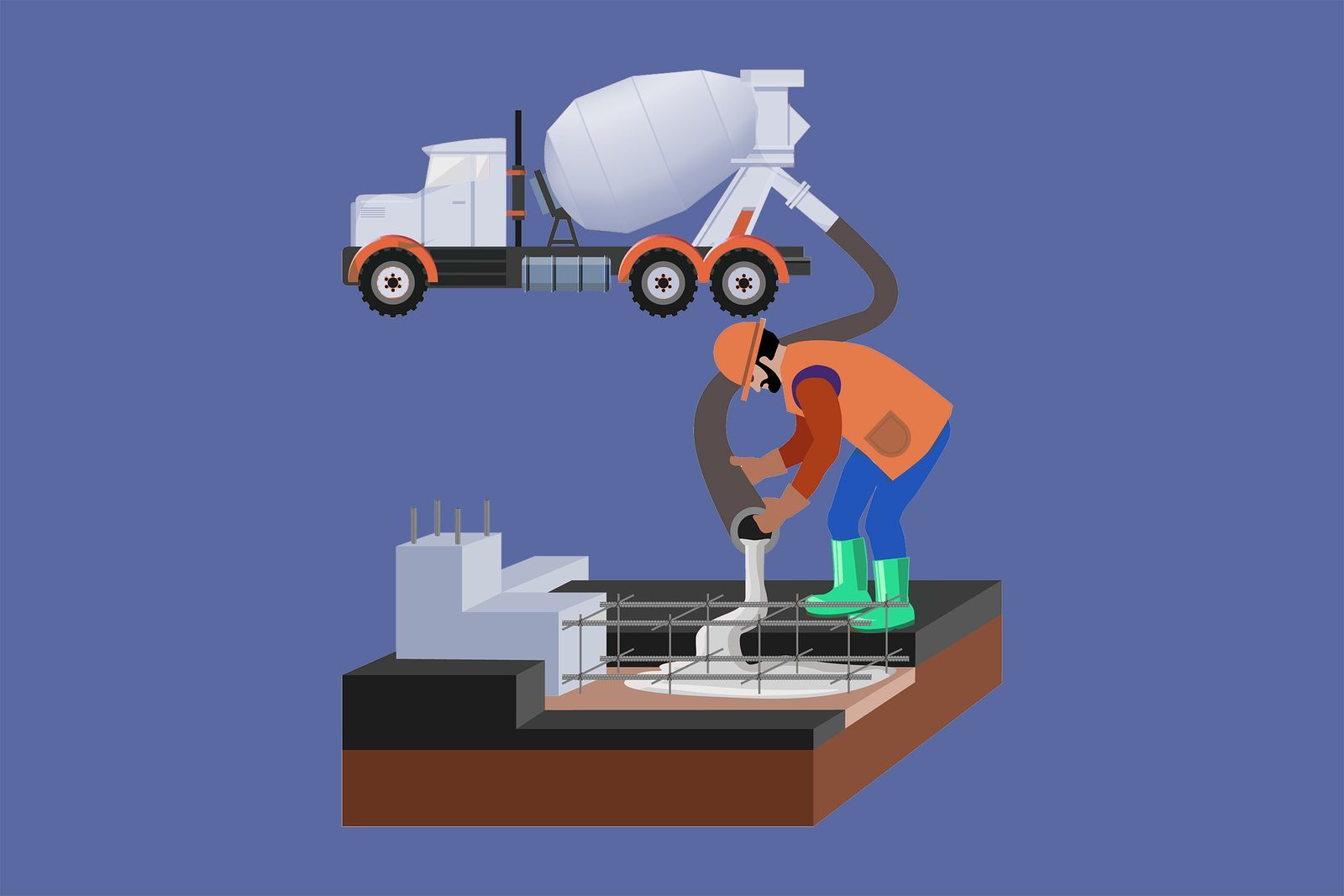
Need a concrete takeoff guide? We break down materials, labor, and profit steps to help you create accurate bids and win profitable projects.
How to Perform a Concrete Takeoff
With annual production in the area of 4.1 billion metric tons, cement is a big deal--used in everything from foundations, structures, pre-cast and cast-in-place panels to stucco, paving, and so many other aspects of construction. Indeed, so essential is concrete to the construction industry that it provides the basis for over 53,000 contracting companies. Concrete’s high compressive strength makes it ideal for bearing heavy loads and transferring weight throughout the structure. From simple slabs poured in place to extensive multi-story structures that seem to touch the sky, knowing how to calculate an accurate concrete takeoff is essential to your company's ability to complete a profitable project.
But why is developing a detailed and accurate concrete estimate so difficult? For starters, if you over-estimate the quantities of concrete you need, your bid may have an inflated price, which means you’ll lose your bid. Alternatively, underestimating how much concrete is needed may result in the lowest bid that enables your firm to win the project, while you lose profitability. If you order concrete based on inaccurate takeoff numbers, your order is likely to be inaccurate, increasing the likelihood of wasted material or delays while waiting for additional material to be delivered.
Therefore, to ensure your takeoff is the most accurate, you need to understand how to complete the entire takeoff process end-to-end quickly and efficiently. With this in mind, we’ve developed our new guide on how to develop a concrete takeoff.
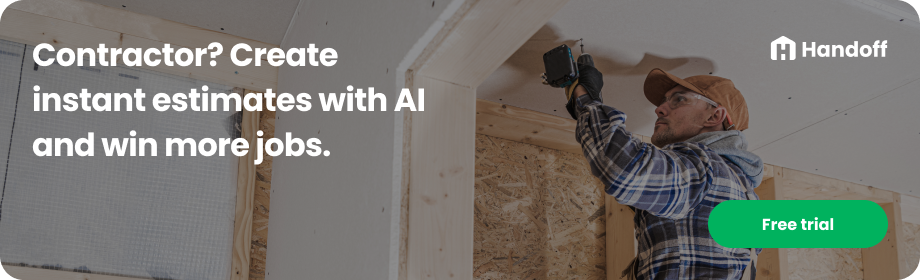
How to Estimate a Concrete Takeoff
Regularly securing projects for your business involves estimating projects that often include a concrete estimate as part of the bid. This means that you'll need to review the plans carefully so that you can calculate the labor and materials needed to complete the project. If you’re unfamiliar with how to prepare a quantity takeoff, check out our post to brush up on the basics of estimating for construction projects.
Because the takeoff is essential to your estimating process, it’s critical that the several steps required to complete a concrete takeoff be handled carefully and methodically. Below we provide the 4 essential steps to completing an accurate concrete takeoff.
4 Essential Steps
Concrete takeoffs are typically based on several specific areas: labor, materials, overhead, and profitability. Labor covers the amount of time it will take to place and finish the concrete, from setting up forms to finishing up the last of the work. Materials can cover items that will be measured in terms of length, area, and volume, with concrete typically being the main component measured by volume, typically by cubic yards.
Overhead costs can include a wide range of expenses that you need to keep the doors open at your business, but are not directly related to the project. Overhead can include insurance, office staff, vehicles, software, rent, and similar costs that you'll need to pay whether you have active projects to work or not. Once you've calculated these aspects, you need to add profit margin onto the figures, which is vital to keep your company operating and profitable.
Working Through the Takeoff Process
In general, there are approximately 21 areas of concrete work that need to be estimated before starting a concrete project. However, not all projects require all 21 areas and most require only a few. But it’s a good idea to develop your concrete takeoff methodically by going through the list in the order below:
Concrete Takeoff Workflow:
- Column Footings: hand excavated area, forms, concrete.
- Wall Footings: hand excavated area, forms, 2 by 4 keys, concrete.
- Foundation Walls: forms (in 4-foot heights), 2 by 4 keys, slab seat bearing, and concrete.
- Piers Below Grade: forms, concrete.
- Building Slabs On Fill: sand fill, edge forms, expansion joints, finish area, and concrete.
- Exterior Columns: forms, concrete.
- Interior Columns: forms, concrete.
- Exterior Beams: forms, concrete.
- Interior Beams: forms, concrete.
- Shortened Flat Slabs: slab forms, edge forms, finish area, concrete.
- Metal Pan Slabs: slab forms, edge forms, finish area, concrete.
- Slabs On Corrugated Formwork: corrugated formwork, edge forms, finish area, concrete.
- Stairs On Fill: sand fill, form risers, finish tread and riser, concrete.
- Shored Stairs: form risers, stair bottom, finish tread and riser, concrete.
- Stair Landings: forms, finish, concrete.
- Pan Fill Stairs: finish, concrete.
- Misc Concrete in Building: forms, finish, concrete.
- Exterior Sidewalks: sand fill, edge forms, expansion joints, finish, concrete.
- Exterior Paving: sand fill, edge forms, expansion joints, finish, concrete.
- Exterior Strait Curbs: hand excavated area, forms, finish, concrete.
- Exterior Curb & Gutter: hand excavated area, forms, finish, concrete.
Again this is an exhaustive list and because every project’s different, you’ll need to skip any area in this list not pertinent to your project. In other words, if your project doesn’t include exterior curbs, simply skip section 21.
Step 1: Estimating Materials
To calculate the cost of materials, you'll need to use a careful, methodical approach to determine measurements, quantities, and similar information. To start, you'll work on your materials takeoff using the list above. Reviewing the plans, you can start from the bottom of one corner, work across that level, and then move up to the next level, taking care to note every piece of rebar, square-foot of reinforcing mesh, or similar materials.
Once you’ve taken note of every material needed for the project, it’s now time to start estimating how much concrete will be needed and what type.
Although every job is different, whether estimating column footings, wall footings, foundation walls, or slabs, you’ll use the same basic formula. You’ll measure off the area and calculate the volume of concrete needed: length x width x depth. You’ll also want to add in an additional cost for waste and spillage, which is roughly 10% of the total volume.
Formula for calculating volume
Length x Width x Depth (LxWxD)
To determine the amount of bags of concrete you’ll need, simply multiply the bags by the total cost. You can purchase concrete at a store for small projects, but for larger projects, you’ll definitely want to work with a ready-mix supplier.
And finally, you can finish estimating materials by calculating any additional materials needed beyond concrete, such as anchors. If you’re pouring concrete more than five inches deep, you’ll also need to add rebar (reinforcing bar) to help reinforce the entire structure of a commercial-level project or wire mesh for smaller residential projects. Although it's tempting to assume you’ll be calculating the cost of stainless steel rebar, there are five basic types of rebar to choose from with considerable price differences, including welded wire fabric, expandable metal, sheet metal, and epoxy coated rebar.
Beyond basic materials, you’ll need to think through other equipment you’ll need for the job and their costs. Here is a list of standard equipment you’ll need for most concrete projects:
Concrete Construction Equipment:
- Mixers
- Floats
- Shovels
- Digging Bars
- Edgers
- Compactors
- Screeds
- Groove Cutters
- Rubber Boots & Gloves
- Polishers
- Wheelbarrows
- Vapour Retarders
- Saws
- Levels
- Brooms
Once you have a general idea of the cost of materials and made notations on the plans, you need to finalize the complete count of materials and their and their costs. Some companies still use paper and pencils, marking off areas on the plan as they complete their counts, though items can be marked off inaccurately. Others use PDF formats of plans and a spreadsheet, but it's fairly easy to accidentally change a formula on the spreadsheet, making errors problematic. Professional estimating software is an option, but it can be costly and has a long learning curve. Another great option is to use an app that does cost estimates with AI like Handoff.
Step 2: Estimating Labor
Now that you’ve determined how much material is needed and its cost, you'll need to think about how long it will take to complete the project in terms of hours of labor and factor in the cost of that labor to your concrete takeoff. While calculating the labor involved, make sure to take into account shift differentials, union or non-union wages, overtime, time spent traveling up or down multi-story structures and similar aspects of the project that can impact labor costs.
It’s also wise to base your figures on how many square feet of work an average worker can do in a day rather than base it on your most productive worker because once you know that, you can estimate labor costs no matter the season or year. A good rule of thumb is to assume an average worker can complete about 300 to 350 square feet of concrete work a day.
In general, you’ll need to add all of the following labor hours (and associated costs) to your concrete takeoff:
- Mixing: the cost to transport mixed concrete into the mixer and the cost of a mixer itself
- Transportation: the cost to transport mixed concrete to the location
- Compaction: the cost involved in using compaction machines/vibrators
- Reinforcement: the cost of steel and labor for cutting and tying of rebars
- Formwork: the cost of formwork for beams, columns, or slabs
- Skilled Labor: the manpower required to mix, transport, compact, and finish concrete but also be factored into the labor cost
Step 3: Determining Overhead
The next step is to add in overhead costs. Overhead costs are any costs incurred that are not related to labor, direct materials, or production, such as running your back office, vehicles, upkeep, advertising, and other expenses. And don’t forget your time meeting with the client and preparing the estimate! That’s all part of what has to be billed.
Calculating overhead can be intimidating at first, but it’s not too difficult. First, you have to know what your overhead expenses are for a year. Include all salaries for anyone who works on the business's back end, like the bookkeeper or secretary.
For larger overhead expenses such as a work vehicle or truck lease, you can also prorate the expense and include it as a cost on your concrete takeoff. For example, if you have a truck that you use regularly for your business and expect it to last 10 years, your yearly cost is 10% of the total cost (1 out of 10).
If you know your total annual overhead expenses, you can also determine what percent of the year you’ll work on a specific concrete project and then factor that percentage into your concrete estimate costs. If your concrete job will last 4 weeks on a large project and you typically work 50 weeks a year, you’ll know that the current takeoff should include 8% of your total overhead expense.
Step 4: Calculating Profitability
And of course, you need to make a profit. How much do you expect to make for the year, above and beyond your expenses? If you want to stay in business, you absolutely need to include markup in your final takeoff.
To factor in profit, start by determining the overall margin for your business, usually somewhere between 2 and 10% in the construction industry, and then include a percentage of this total annual number just like you did for overhead costs.
Of course, when you write up your final takeoff, estimate, or quote, you won’t include sections for “overhead” and “profit”. Instead, you’ll fold these costs into labor costs on your final concrete takeoff.
Considerations When Performing Concrete Takeoff
When you're undertaking a concrete takeoff, there are many important considerations that you should take into account that can impact your estimate:
- Is the project a good fit for your company's experience? If you've done a lot of shotcrete as your mainstay, going to a large paving or pump and fill project may be problematic. It may not be a good fit for your knowledge base, experience, and skill set. Though it's okay to use these approaches to break into new market sectors with the potential for profit loss and a solid learning curve, it's better to start small and pass on projects that won't be a good fit. Keep with what you know to get the work done efficiently and profitably.
- Look at the plans for anything odd, unique or unusual. If you need to add special labor, materials, or other resources, try to determine if you can complete that part of your project while making a profit. Consider subcontracting that part if it's going to tie your crew down. Adding a change order later for something you missed on the plans during the takeoff stage can look unprofessional.
- Start at the bottom with anchors, rebar, reinforcing mesh, and similar materials. Some companies will use different colored markers, pencils, and pens to mark up paper plans, then transfer the counts they've made to a separate list. If you try this, make sure you're consistently marking up the plans the same way, then double-check the work to make sure it's correct.
- Look at what type and how much concrete will be needed. Does that slab need to be 3,000 or 5,000 PSI? What about those high-strength columns? Look at all of the different areas you'll need to be worked on, then calculate each area and type of concrete to be able to calculate the cubic yardage, then reach out to your suppliers to determine the cost of the materials.
- Do you need any unusual materials? If the project calls for colored concrete, reinforcing fibers, or other materials that are not usual, make sure that you take a careful look at the specifications. Do the materials need special handling? Will you need to bring in additional labor to get the job done right? Take a close look at issues such as these to make sure they don't eat into your profits.
- What about odd parts of the project that will require more or specialized labor? If you need to take special care to finish up a particular project, need to hire a subcontractor to handle a specialty concrete product, or have to pay overtime or a shift differential for a highway job that can only be poured at night, make sure that you note it in your takeoff. You could also consider specialty offsets for LEED construction under these areas.
- Once you've completed your takeoff, walk away, then review your calculations or have someone else check them for accuracy. Do you have accurate supplier costs? Are the labor and material takeoffs reasonable? Take the time to walk through the plans mentally to see if you've missed anything. This could be as simple as water tanks for a remote peagravel pour, excavation equipment rentals, or similar aspects.
Concrete Takeoff Services Save Time and Eliminate Errors
While we’ve just provided a detailed guide on how to complete an accurate concrete takeoff or estimate, the process is complicated, time-consuming, and stressful. Beyond determining your materials and labor, you’ll have to answer so many questions during the process. What should your overhead be? How much profit should you add? What do you need to include with the paperwork to submit the final proposal? You probably didn't get into business for all of this hassle.
When it comes to your concrete business, what you do best is run your company and get concrete placed and finished. What if you could continue to focus on those aspects of your business while still keeping a regular stream of projects coming through the door without having to split your attention to the next five projects you need to bid?
If you work with Handoff, you'll be able to do just that. Our estimating AI can take care of making sure you've got a solid, accurate concrete estimates that takes into account the many factors of each project that makes it unique and difficult to bid.